Обкатка и испытание двигателей обычно выполняются в три стадии. Первая стадия — холодная обкатка, когда коленчатый вал двигателя принудительно приводится во вращение от электродвигателя; вторая — горячая обкатка работающего двигателя без нагрузки; третья — горячая обкатка под нагрузкой работающего двигателя. Обкатку и испытания двигателей проводят по режимам в соответствии с требованиями технических условий. Завершают обкатку двигателей снятием контрольной точки развиваемой им мощности на тормозном стенде.
Совершенствование процессов обкатки и испытания отремонтированных двигателей идет по пути использования электрических стендов (разработки ГОСНИТИ), систем централизованной смазки, а также средств частичной и комплексной автоматизации процессов и устройств, обеспечивающих режимы обкатки и поддержание стабильного теплового режима двигателя.
При достаточно высоком уровне технологической дисциплины ремонта двигателей создаются условия для автоматизации процесса обкатки. Устройство автоматического управления режимами обкатки (рис. 2.23) позволяет управлять жидкостным реостатом стенда и дроссельной заслонкой (или топливным насосом) двигателя, обеспечивая плавное изменение частоты вращения коленчатого вала и нагрузки. Работа оператора при этом сводится к запуску стенда, установлению автоматизирующего устройства в исходное положение холодной обкатки и по сигналу ее окончания — к переключению устройства на следующий этап — горячую обкатку. После окончания приработки электротормозной стенд выключается конечным выключателем.
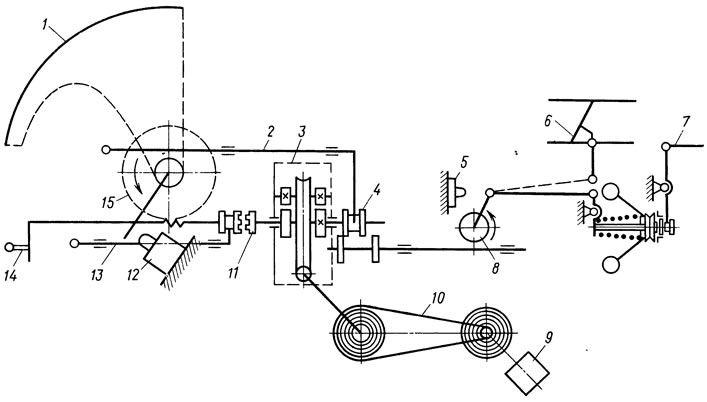
Рис. 2.23. Кинематическая схема механизмов автоматического управления приработкой двигателей: 1 - электрод реостата; 2 - тяга переключения зубчатой передачи; 3 - планетарный редуктор; 4 - зубчатая передача; 5 и 12 - конечные выключатели; 6 - воздушная заслонка; 7 - тяга к рейке топливного насоса; 8 и 15 - червячные передачи; 9 - электродвигатель; 10 - ременная передача; 11 - кулачковая муфта; 13 - тяга включения кулачковой муфты; 14 - ручка реостата
Поддержание требуемой температуры воды и масла обеспечивается при помощи терморегулятора (рис. 2.24). Вода в баке 7 и масло в баке 11 прогреваются электронагревателями 9 и 14 при включении терморегулятора в сеть рубильником 1, При этом контакты 2 и 3 термометра ТС-100 замкнут цепи реле 10 и 13, включающих подогрев соответственно воды и масла. В водяную рубашку 4 и картер 6 двигателя установлены датчики 5 термометров воды и масла. При достижении заданной температуры контакты термометров разомкнутся и подогрев прекратится. В случае повышения температуры выше требуемой замкнется вторая пара дистанционных термометров ТС-100 и включатся реле 18 и 16, которые включат электромагнитные краны 75 и 17 охлаждения воды и масла соответственно. Охлаждающая вода будет поступать до момента, когда температура воды и масла в обкатываемом двигателе не будет в пределах заданных значений. Перекачка воды и масла производится при помощи насосов 8 и 12 соответственно. При повышении температуры процесс регулирования повторяется.
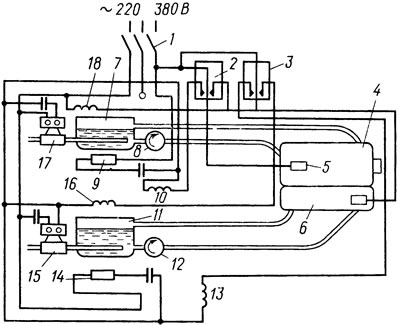
Рис. 2.24. Схема устройства для автоматического регулирования температуры воды и масла при обкатке двигателей
При обкатке и испытании дизелей применяют топливо и масло летних сортов, рекомендуемые инструкцией по эксплуатации для дизелей данной модели. У двигателя, подготовленного к обкатке и испытанию, наружные поверхности должны быть чистыми и сухими, особенно в местах соединений деталей и уплотнений, вокруг заглушек и заваренных мест.
В настоящее время многие АТП в своих мастерских заменяют поршневые кольца, вкладыши подшипников коленчатого вала, а во многих случаях выполняют и капитальные ремонты. При этом обкатка, как правило, не производится дли производится только на холостом хода; что не дает нужных результатов. При восстановлении работоспособности автомобильных двигателей заменой изношенной гильзо-поршневой группы, коленчатого вала с вкладышами приработка и испытание так же необходимы, как и для капитально отремонтированных двигателей в условиях ремонтного предприятия. Особенно важное значение имеет приработка при замене поршневых колец.
В настоящее время не каждое АТП располагает обкаточно-тормозными стендами и вряд ли следует считать целесообразным их приобретение. Практике известны более простые и доступные методы обкатки и испытания автомобильных двигателей, не требующие сложного и дорогостоящего оборудования. Это так называемые бестормозные обкатка и испытание, при которых в качестве нагрузки служат собственные сопротивления двигателя в сочетании с выключением части цилиндров, ограничение нагрузки постановкой шайбы во впускной трубопровод карбюраторного двигателя или ограничение хода рейки топливного насоса дизельного двигателя. При выключении из работы одного или нескольких цилиндров часть индикаторной мощности расходуется на преодоление трения в деталях цилиндропоршневой группы, кривошипно-шатунного и других механизмов, а также насосных потерь, выключенных и работающих цилиндров. Этим и создается нагрузка на двигатель. Внешней нагрузкой для работающих цилиндров в данном случае будут механические и насосные потери выключенных цилиндров. Поэтому ее принято называть бес-тормозной нагрузкой.
Исследованиями установлено, что тормозные и бестормозные обкатки дают примерно одинаковые результаты. Например, при выключении четырех цилиндров двигателя ЗИЛ-130 бестормозная нагрузка изменяется в пределах от 9,7 кВт при частоте вращения коленчатого вала 800 мин-1 до 52,2 кВт при частоте 2800 мин-1, что примерно соответствует тормозной нагрузке при обкатке этих двигателей в АРП. Для бестормозной обкатки, например, карбюраторного двигателя, необходим приводной стенд с электродвигателем, обеспечивающим частоту вращения коленчатого вала 500...1000 мин-1, и оснастка для выключения из работы части цилиндров и ограничения впуска рабочей смеси в цилиндры.
Другие агрегаты автомобиля после сборки подвергают испытаниям по режимам, предусмотренным техническими условиями на КР автомобиля. Целью испытаний агрегатов является проверка качества их сборки и готовности агрегата к работе. Испытания выполняются на различных стендах, оборудованных тормозными устройствами. Наиболее перспективными для авторемонтного производства являются электрические стенды с электромагнитными нагрузочными устройствами.
При испытании коробки передач проверяют работу шестерен на всех передачах, легкость включения и отсутствие самопроизвольного выключения передач. Время испытания составляет 20...25 мин, в том числе под нагрузкой 12...15 мин при частоте вращения ведущего вала 1000—1400 мин-1. Задние мосты также испытывают без нагрузки и под нагрузкой. При этом регулируют тормозные механизмы и проверяют работу главной передачи и дифференциала.
Нагрев масла и деталей агрегатов при испытаниях зависит от качества их сборки: перекоса осей валов, зацепления шестерен, регулировки подшипников и т. д. Определяют нагрев деталей и масла с помощью несложных электронных приборов с полупроводниковыми датчиками типа ММ1. Для контроля нагрева можно использовать термокраски, которые изменяют свой цвет при нагреве свыше 60°C. Для измерения вибраций лучшими являются виброакустические методы. Шумы и стуки в испытуемых агрегатах определяют с помощью шумомеров.