Топливные баки
Топливные баки изготавливают из стали 08. Основные дефекты их: вмятины, разрывы и трещины в стенках или в местах крепления заливной горловины и штуцеров; нарушения крепления перегородок со стенками бака.
При общей площади пробоин и сквозных коррозионных разрушений более 600 см2 бак бракуется. При меньшей площади повреждений бак восстанавливают постановкой заплат с последующей их приваркой или припайкой твердыми припоями. Перед восстановлением баков сваркой их выпаривают в течение 3 ч до полного удаления паров топлива.
При значительной вмятине на противоположной стороне бака вырезают прямоугольное окно с трех сторон по периметру и отгибают вырезанную часть стенки так, чтобы был свободный доступ инструмента внутрь бака. При помощи оправки и молотка выправляют вмятину и одновременно приваривают нарушенное крепление перегородки. Затем отогнутую часть стенки возвращают на место и заваривают.
Небольшие трещины устраняют пайкой низкотемпературными припоями, большие — пайкой высокотемпературными припоями, а в некоторых случаях и постановкой заплат.
Топливопроводы
Топливопроводы низкого давления изготавливают из латунных или стальных трубок с антикоррозийным покрытием, топливопроводы высокого давления — из толстостенных стальных трубок. Основные дефекты их: трещины, перетирания, переломы, вмятины, повреждения соединительных концов.
Трещины, перетирания и переломы топливопроводов низкого давления устраняют припайкой муфты, которую изготовляют из трубки большего диаметра, чем ремонтируемая (рис. 4.15). Концы топливопроводов высокого давления сваривают газовой сваркой встык, предварительно обрабатывая на них фаски под углом 45°.
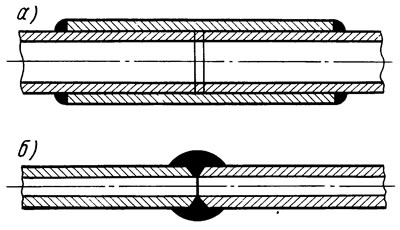
Рис. 4.15. Способы соединения топливопроводов низкого (а) и высокого (б) давления
Вмятины на топливопроводах вырезают, а оставшиеся части соединяют вышеуказанными способами. Вмятины также устраняют правкой путем прогонки шарика. Поврежденные соединительные концы топливопроводов отрезают и вновь развальцовывают при помощи специального приспособления.
Бензонасосы
Корпус, головка и крышка-демпфер бензонасоса изготавливаются из цинкового сплава.
Корпус бензонасоса может иметь износ отверстий под ось рычага привода, срыв резьбы, коробление плоскости разъема корпуса с крышкой. Изношенные отверстия под ось рычага привода развертывают и устанавливают новую ось увеличенного размера или устраняют износ постановкой втулки с последующим ее развертыванием в соответствии с размером на чертеже. Сорванную резьбу в отверстиях восстанавливают нарезанием резьбы ремонтного размера. Коробление плоскости разъема устраняют притиркой на плите абразивной шкуркой или пастой. При наличии обломов и трещин любого характера корпус, головку и крышку заменяют.
В рычаге привода насоса изношенное отверстие под ось развертывают до большего диаметра, а рабочую поверхность наплавляют и обрабатывают по шаблону.
Карбюраторы
Корпус и крышку карбюратора изготавливают из цинкового сплава. Основные дефекты карбюратора: потеря герметичности поплавка; износы запорного игольчатого клапана, проходных сечений жиклеров, иглы главного жиклера, гладких и резьбовых отверстий; трещины и обломы.
После выдержки в ванне с керосином в течение 25...30 мин и очистки щеткой карбюратор разбирают на специальных приспособлениях. Детали промывают в ваннах с керосином и продувают сжатым воздухом. Для очистки от смолистых отложений жиклеры, клапана, распылители промывают в ацетоне или нитрорастворителе, после чего продувают сжатым воздухом.
Герметичность игольчатого клапана восстанавливают притиркой; при большом износе его заменяют в сборе с седлом. Герметичность поплавка проверяют погружением в ванну с водой при температуре 70...80°C и выдержке в ней в течение 1 мин. Место появления пузырьков воздуха расширяют шилом и выпаривают бензин, попавший внутрь поплавка. Вес поплавка после пайки должен соответствовать техническим требованиям.
Жиклеры проверяют на пропускную способность. Изношенные жиклеры заменяют новыми.
Корпус карбюратора, имеющий трещины и обломы, выбраковывают. Коробление привалочных плоскостей корпуса устраняют притиранием на плите или припиливанием и шабрением. Изношенные отверстия под оси развертывают под ремонтный размер или под постановку бронзовых втулок. Поврежденную резьбу под винты крепления восстанавливают нарезанием резьбы большего размера.
Топливные насосы высокого давления
Топливную аппаратуру моют в ванне с керосином, очищают волосяными щетками, а затем разбирают. Плунжер с гильзой, нагнетательный клапан с гнездом, корпус распылителя с иглой не разукомплектовываются.
Корпус топливного насоса высокого давления изготавливают из серого чугуна или алюминиевого сплава. Он имеет следующие основные дефекты: обломы, трещины, износы отверстия под толкатели, гладких и резьбовых отверстий.
Обломы и трещины, захватывающие отверстия под подшипники, штуцера и внутренние перемычки являются выбраковочными признаками. Остальные трещины устраняют эпоксидными композициями. Не рекомендуется устранять трещины сваркой, так как нагрев может вызвать деформацию и нарушение соосности посадочных поверхностей.
Износ отверстий под толкатели плунжеров устраняют обработкой их под ремонтный размер, а износы под опоры кулачкового вала и ось промежуточной шестерни восстанавливают постановкой втулок.
При восстановлении поврежденной резьбы для крепления деталей рекомендуется постановка ввертышей из латуни или пружинных вставок.
Кулачковый вал изготавливается из стали 45 с последующей закалкой кулачков и опорных шеек до твердости 53...63 HRC3. Основными дефектами являются износы поверхности кулачков, опорных шеек, шпоночной канавки и резьбы.
Незначительный износ кулачков устраняют шлифованием на копировально-шлифовальном станке. Изношенные опорные шейки восстанавливают вибродуговой наплавкой с последующим шлифованием в соответствии с размером на чертеже. Шпоночную канавку и резьбовые концы вала восстанавливают наплавкой с последующей механической обработкой, обеспечивая размер по чертежу.
Детали плунжерной пары (рис. 4.16, а) промывают в дизельном топливе и проверяют их состояние с помощью лупы. Плунжерные пары с гладкой поверхностью подвергаются предварительной проверке на свободу перемещения плунжера и герметичность. Плунжерные пары, не обеспечивающие герметичность, разукомплектовывают. Гильзы и плунжер с изношенными поверхностями, рисками и следами коррозии ремонтируют. Повреждения на торцевой поверхности гильзы устраняют притиркой на чугунной плите пастой ГОИ. Для получения правильной геометрической формы и необходимой шероховатости производят предварительную и окончательную обработку поверхности плунжера гильзы чугунными притирами. Затем детали плунжерной пары комплектуют таким образом, чтобы плунжер плотно входил в гильзу на 1/3 рабочей зоны, и обеспечивают взаимную притирку. Не допускается обезличивание притертой плунжерной пары после промывки в бензине.
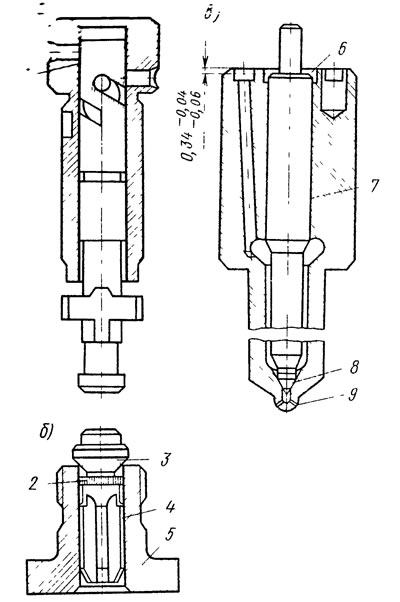
Рис. 4.16. Обрабатываемые поверхности: а - плунжерной пары; б - нагнетательного клапана; в - распылителя форсунки; 1 - направляющая поверхность плунжера и втулки плунжера; 2 - разгрузочный поясок клапана; 3 - конусная поверхность клапана; 4 - направляющая поверхность клапана и седла; 5 - торец седла клапана; 6 - торцевая поверхность корпуса распылителя; 7 и 8 - соответственно направляющая и конусная поверхности иглы и корпуса; 9 - сопловые отверстия
В деталях нагнетательного клапана (рис. 4.16, б) основными дефектами являются риски, следы износа и коррозии. Повреждения на торцевой поверхности седла клапана устраняют притиркой на чугунной плите. Повреждения конусных и цилиндрических поверхностей устраняют взаимной притиркой. Если притирка не устраняет глубоких рисок или следов выработки, детали клапана бракуют.
Форсунки
Корпус распылителя форсунки (рис. 4.16, в) очищают с наружной поверхности от нагара латунной щеткой, а сопловые отверстия прочищают стальной проволокой диаметром 0,30 мм и контролируют их калибром диаметром 0,37 мм. Если калибр проходит хотя бы в одно из отверстий, корпус распылителя бракуют. Также подлежат выбраковке распылители со следами оплавления носика. Внутреннюю полость корпуса распылителя очищают латунными скребками, а вертикальный канал — медной проволокой диаметром 1,5...2,0 мм. Риски и следы коррозии на торцевой поверхности устраняют притиркой на притирочных плитах. Риски и следы износа на направляющей и конусной поверхностях отверстий удаляют при помощи притиров, доводя эти поверхности до требуемой геометрической формы и шероховатости и затем сортируют на группы по диаметру отверстий.
Иглы распылителя обрабатывают притирами до удаления следов износа и рисок на направляющей и конической поверхностях. Сортируют иглы на группы по диаметру направляющей, подбирают к распылителям и притирают их друг к другу, предварительно нанеся пасту ГОИ на цилиндрическую поверхность иглы. Затем притирают конические поверхности. После притирки детали промывают в дизельном топливе и контролируют их относительное расположение в закрытом состоянии. Расстояние между торцами корпуса распылителя и иглы должно быть (0,34-0,04) мм. Этот размер обеспечивается доводкой торца корпуса распылителя.